November 16, 2021
Artificial intelligence helps ŠKODA AUTO with the best space utilization of containers
ŠKODA AUTO is constantly improving its products and customer services. It does not lag even with increasing efficiency and optimizing processes, including those in and outside production halls. Every week, the car manufacturer despatches around two thousand pallets full of components and materials. Optimization algorithms packaged in the OPTIKON application, created in collaboration with Blindspot.AI, help with sea container space utilization and efficient pallet handling and arrangement in container space.
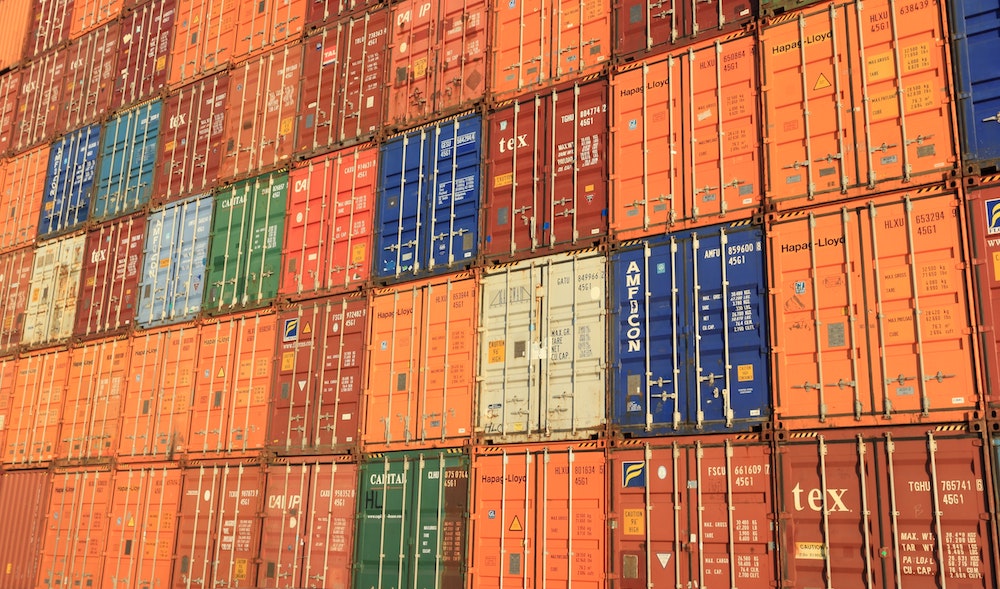
Solution to a problem
From the logistics center in Mladá Boleslav, containers loaded with pallets full of components intended for the assembly of cars abroad are shipped. The car manufacturer handled and managed the loading of containers using instruction manuals and employees' experience. Employees always tried to put together the ideal combinations of different sizes of loaded pallets, but it was often not easy and possible to look after:
- Containers to not be loaded with more spatially suitable pallets primarily.
- More efficient loading of even less spatially suitable pallets.
- The correct weight distribution in containers that are loaded with less suitable pallets.
However, finding new pallet loading combinations was becoming more complicated, and, at the same time, it was more difficult for manufacturers to approach the set loading criteria.
Business description of the solution
There are many limiting and other conditions that need to be taken into account when optimizing loading. These include the time required to calculate a suitable pallet combination. In this case, the logistics processes limit the time to 30 seconds. However, the current course of planning the loading of containers took more time and offered lower efficiency.
At the beginning of 2019, therefore, ŠKODA AUTO joined forces with Blindspot. Together, we began working on a proof of concept and subsequent testing of technology that would improve the process. The OPTIKON system was created, thanks to which workers can easily find out the best possible stacking of pallets into a container using a tablet.
OPTIKON calculates the optimal number of different types of used pallets, which the car manufacturer uses around two thousand, and suggests the best way of their placement in a container. The system considers the dimensions and weight of the pallets, the material on the pallets and ensures that the total weight in the container is correctly distributed. The application is also able to check whether the pallets that are to be loaded and shipped in a given week are actually loaded into the right container.
The solution is deployed in the Microsoft Azure cloud ecosystem and is built on top of the Optim-AI optimization platform, on which we also worked together. The first phase (PoC and testing) of the project took only three months. The whole OPTIKON system was deployed in a production environment a few months later in the same year.
Project outcome
By deploying optimization algorithms packaged in the OPTIKON application and digitizing the loading planning process, together with the major Czech automotive manufacturer, we have achieved:
- savings of EUR 840,000 during the first year,
- savings in shipping 300 containers during the first year
- savings of 162 tons of CO2 emissions during the first year
- facilitating the process of training new employees
- options to detect system loafing errors
ŠKODA AUTO wants to offer the OPTIKON system to other brands within the group to also take advantage of the help and benefits of artificial intelligence.